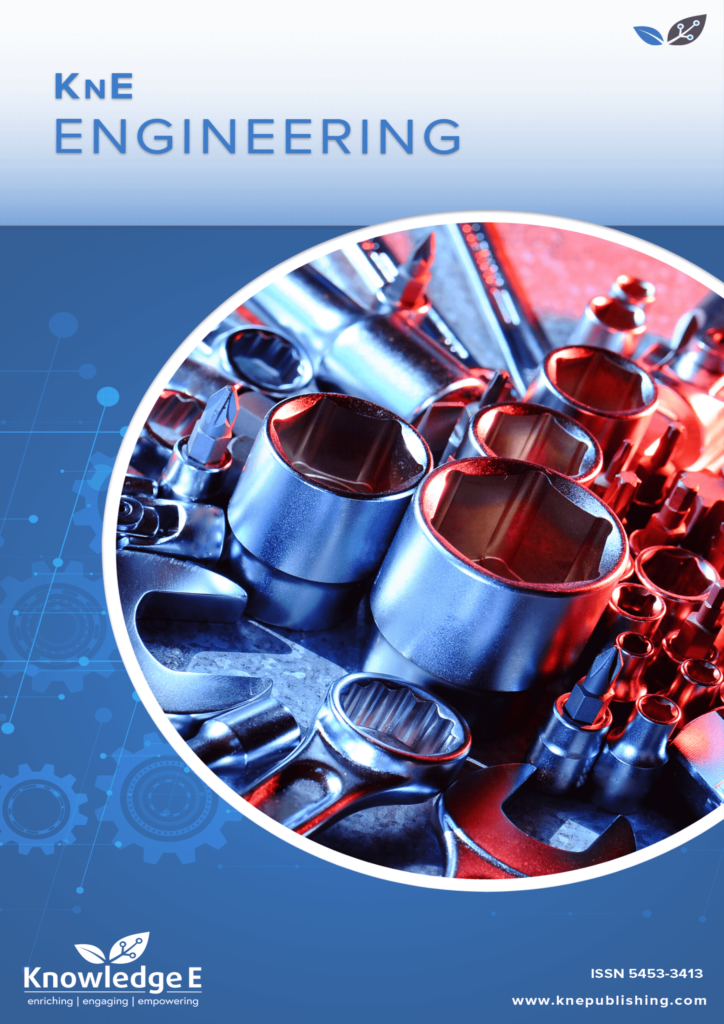
KnE Engineering
ISSN: 2518-6841
The latest conference proceedings on all fields of engineering.
Structure of the Optimal Management System for Raw Materials, Fuel and Energy Resources in Blast-furnace Production
Published date:Jul 17 2018
Journal Title: KnE Engineering
Issue title: VII All-Russian Scientific and Practical Conference of Students, Graduate Students and Young Scientists (TIM'2018)
Pages:118–130
Authors:
Abstract:
The structure of optimization model of optimal management of raw materials, fuel and energy resources in the blast-furnace shop of iron and steel works is represented. The following blocks are taken as system basis: (1) calculation of the set of parameters that characterize the thermal, gas-dynamic, slag and blasting modes for every blast furnaces of the shop during the base period; (2) calculation of linearized model coefficients (constants of transferring via different exposure pathways) individually for every blast furnace as well as properties of iron ore raw materials, fluxing additions, blasting parameters, parameters of fuel-enriched blast influencing the technical-and-economic indices of separate furnaces performance, their thermal, gasdynamic and slag operation modes in the course of blast-furnace melting according to UrFU-MMT blast-furnace production model within the base period; (3) solution of tasks that consider the optimal allocation of raw materials, fuel and energy resources for the project period of blast furnaces operation; (4) analysis of obtained results and providing of recommendations on the optimization of blast furnaces parameters. The developed functional model of optimal distribution of raw materials, fuel and energy resources for the engineering and technology personnel of blast-furnace shop is illustrated; the main functions and interconnections between the separate functional blocks are defined. The functions of created ‘Optimal management of raw materials, fuel and energy resources in the blast-furnace production’ software that is realized in the Microsoft Visual Studio 2017 (С# programming language) programming environment in the form of web application are pointed out. The program product provides the engineering and technology personnel of blast furnace shop of iron and
steel works with the opportunity to solve the tasks of optimal distribution of fuel and energy resources (natural gas and oxygen consumption) within the group of blast furnaces in the different technological situations.
Keywords: blast-furnace production, resources distribution optimization, fuel and energy resources, raw material resources, functional modeling, decision support system, software development
References:
[1] Porzio, G. F., Colla, V., Matarese, N., et al. (2014). Process integration in energy and carbon intensive industries: An example of exploitation of optimization techniques and decision support. Applied Thermal Engineering, vol. 70, no. 2, pp. 1148–1155.
[2] Bandyopadhyay, S. and Sahu, G. C. (2011). Minimization of resource requirement and inter-plant cross flow across resource allocation networks. Chemical Engineering Transactions, vol. 25, pp. 279–284.
[3] Froehling, M., Schwaderer, F., Bartusch, H., et al. (2010). Integrated planning of transportation and recycling for multiple plants based on process simulation. European Journal of Operational Research, vol. 207, no. 2, pp. 958–970.
[4] Ganjehkaviri, A., Mohd Jaafar, M. N., Ahmadi, P., et al. (2014). Modelling and optimization of combined cycle power plant based on exergoeconomic and environmental analyses. Applied Thermal Engineering, vol. 67, no. 1–2, pp. 566–578.
[5] Martin, E., Meis, M., Mourenza, C., et al. (2012). Fast solution of direct and inverse design problems concerning furnace operation conditions in steel industry. Applied Thermal Engineering, vol. 47, pp. 41–53.
[6] Kuang, S., Li, Z., and Yu, A. (2018). Review on modeling and simulation of blast furnace. Steel Research International, vol. 89, no. 1, Code UNSP 1700071.
[7] Ariyama, T., Natsui, S., Kon, T., et al. (2014). Recent progress on advanced blast furnace mathematical models based on discrete method. ISIJ International, vol. 54, no. 7, pp. 1457–1471.
[8] Spirin, N. A., Lavrov, V. V., Yu, V., et al. (2011). Model Systems of Decision Support in CAPCS of Metallurgical Blast-furnace Melting, N. A. Spirin (ed.), p. 462. Yekaterinburg: UrFU.
[9] Spirin, N. A., Lavrov, V. V., Burykin, A. A., et al. (2011). Complex of model systems for supporting decisions made in managing blast-furnace smelting technology. Metallurgist, vol. 54, no. 9–10, pp. 566–569.
[10] Spirin, N., Gileva, L., Lavrov, V., et al. (2015). The pilot expert system to control blast furnace operation. AISTech 2015 Iron and Steel Technology Conference and 7th International Conference on the Science and Technology of Ironmaking, ICSTI 2015. Cleveland, United States,. Code 113707, vol. 1, pp. 1225–1232.
[11] Spirin, N. A., Lavrov, V. V., Rybolovlev, V. Y., et al. (2016). Use of contemporary information technology for analyzing the blast furnace process. Metallurgist, vol. 60, no. 5–6, pp. 471–477.