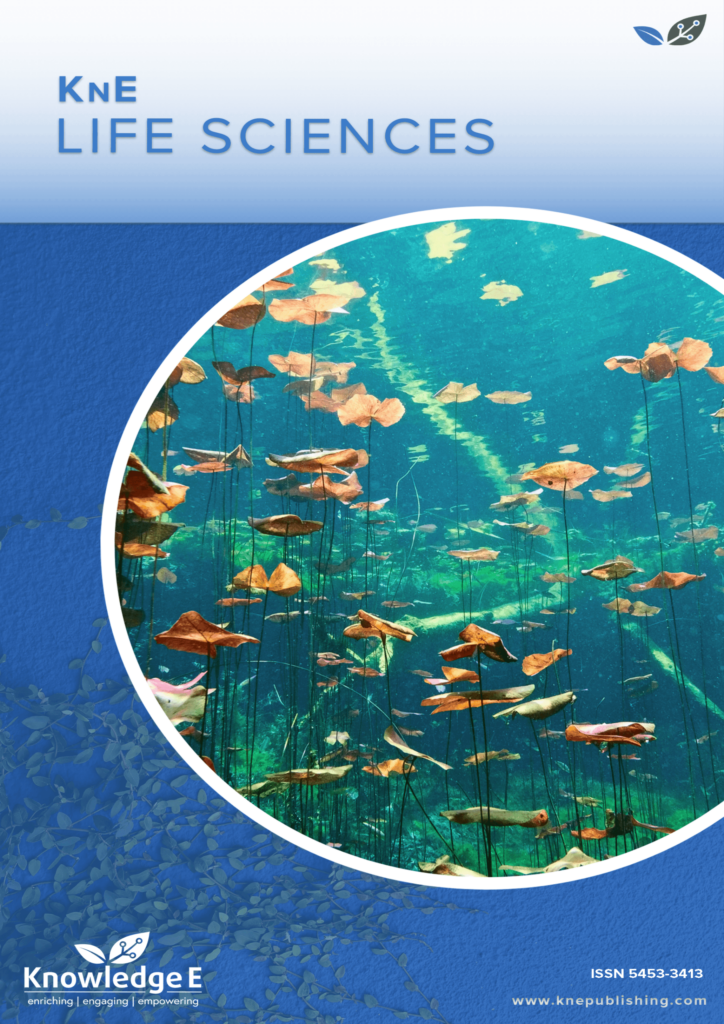
KnE Life Sciences
ISSN: 2413-0877
The latest conference proceedings on life sciences, medicine and pharmacology.
Plasma Torch Working Gas Selection Rationale for the Production Technology of Ultrapure White Corundum
Published date: Apr 05 2021
Journal Title: KnE Life Sciences
Issue title: DonAgro: International Research Conference on Challenges and Advances in Farming, Food Manufacturing, Agricultural Research and Education
Pages: 247–254
Authors:
Abstract:
This paper presents the results of one of the stages in the development of a plasma technology for producing ultrapure white corundum. This technology involves the melting of alumina in a reactor under the influence of plasma. To create the plasma, a plasma-forming gas is needed; in other words, the plasma torch working gas. To implement this technology, the chosen working gas must meet certain requirements. More precisely: 1) the gas should not form explosive or toxic compounds either with the reactor materials or the material of the electrodes; 2) it should not accelerate their erosion. An important requirement that a plasma torch working gas must have is minimal interaction with surrounding substances, even at high temperatures. This will reduce the likelihood of contamination of the melt with materials of the reactor itself. We consider using hydrogen, nitrogen and argon. Taking into account the requirements for the working gas, we opt for the mixture of nitrogen and argon at a concentration of 25÷30% N2 – 70÷75% Ar.
Keywords: plasma torch, corundum, plasma technology, ultrapure materials
References:
[1] Vetyukov, M. M., Cyplakov, A. M. and Shkolnikov, S. N. (1987). Electrometallurgy of Aluminum and Magnesium. Moscow: Moscow Publisher, p. 320.
[2] Grjotheim, K. and Kvande, H. (1993). Introduction to Aluminum Electrolysis. Dusseldorf: AluminumVerlag, p. 243.
[3] Mincis, M. Y., Polyakov, P. V. and Sirazutdinov, G. A. (2001). Electrometallurgy of Aluminum. Novosibirsk: Nauka, p. 368.
[4] Boulos, M. I., et al. (1993). Fundamentals of Plasma Particle Momentum and Heat Transfer. In R. Suryanarayanan (Ed.), Plasma Spraying: Theory and Applications. Singapore: Word Scientific Publishing Co. Pte. Ltd., p. 308.
[5] Miheev, M. A. and Miheeva, I. M. (1977). Heat Transfer Basics. Moscow: Energiya, p. 345.
[6] Landau, L. D. and Lifshitz, E. M. (1986). Hydrodynamics. Theoretical Physics (vol. 4). Moscow: Nauka, p. 736.
[7] Huglen, R. and Kvande, H. (1994). Global Considerations of Aluminum Electrolysis on Energy and the Environment. Presented at Proc. of the 123rd TMS Annual Meeting on Light Metals February 27 – March 3, 1994, San Francisco, USA, Minerals, Metals & Materials Soc, p. 373.
[8] Halmann, M., Frei, A. and Steinfeld, A. (2007). Carbothermal Reduction of Alumina: Thermochemical Equilibrium Calculations and Experimental Investigation. Energy, vol. 32, issue 12, p. 2420.
[9] Cox, J. H. and Pidgeon, L. M. (1963). An Investigation of the Aluminum-Oxygen-Carbon System. Canadian Journal of Chemistry, vol. 41, p. 671.
[10] Lacamera, A. F. (2002). Carbothermic Aluminum Production using Scrap Aluminum as a Coolant US Patent 6 475 260.
[11] Homich, V. A., et al. (2010). Modeling the Formation of Atomic Nitrogen in a Glow Discharge Plasma in a Nitrogen-Argon Mixture. Technical Physics Letters, vol. 36, issue 19, p. 91.
[12] CHihraj, E. V., et al. (2010). Investigation of the Interaction of Graphite with Reactive Gases. Presented at Proceeding of International Conference “Interaction of Hydrogen Isotopes with Structural Materials - IHISM’10” July 2010, Voronezh, Russia, Sarov: RFNC - All Russian Research Institute of Experimental Physics, p. 232.
[13] Anufriev, V. I. (2001). Handbook of a Mechanical Engineer (vol. 3). Moscow: Mashinostroenie p. 859.